Cutting Sheet Metal - The Ultimate Guide
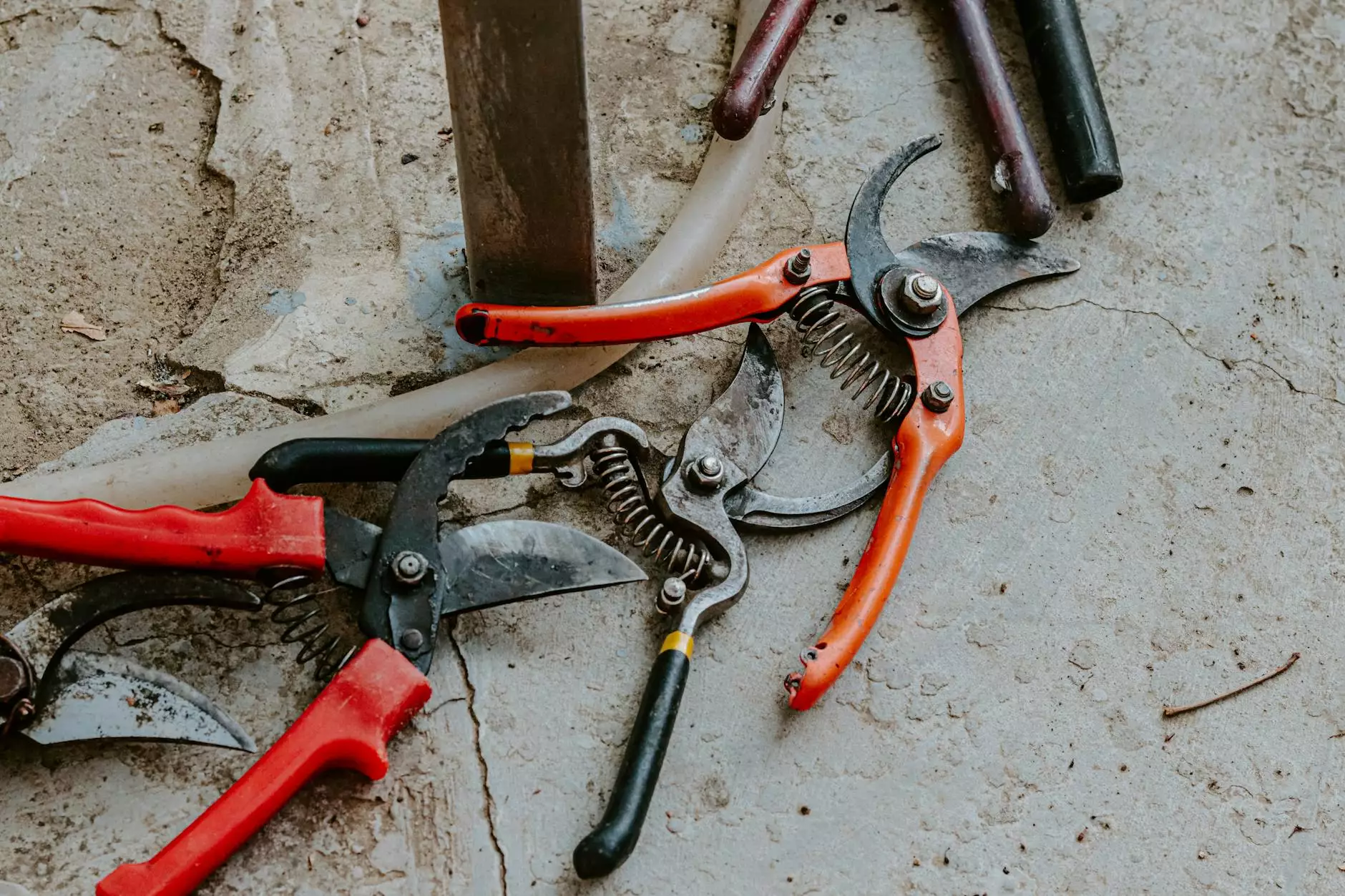
Introduction
Welcome to QuickParts, your go-to resource for all your metal fabrication and 3D printing needs. In this comprehensive guide, we will delve into the intricacies of cutting sheet metal, exploring various techniques, tools, safety precautions, and more. Whether you are a seasoned professional or a beginner in the world of metal fabrication, this article will provide you with valuable insights and knowledge to elevate your cutting skills and ensure exceptional results.
Chapter 1: Understanding the Basics
Before we embark on our journey of mastering sheet metal cutting, it is crucial to grasp the fundamental concepts. Sheet metal is a versatile material extensively used in various industries due to its exceptional strength, durability, and aesthetic appeal. It typically comes in flat, thin pieces, ranging from extremely thin foils to thick plates, and can be fabricated into countless shapes and sizes.
1.1 Sheet Metal Thickness and Precision Requirements
One of the critical factors in sheet metal cutting is the sheet metal thickness. The thickness of the sheet metal determines the appropriate cutting technique and the precision required. Thinner sheets, such as foils, may require delicate and precise cutting methods, while thicker plates might entail more robust and powerful cutting tools.
1.2 Cutting Techniques
Sheet metal cutting involves several techniques, each with its advantages and applications. Let's explore a few of the most commonly used methods:
1.2.1 Shears
Shears are a classic tool used for cutting sheet metal. They consist of two sharp blades that move in a scissor-like motion to cut through the material. Shears are ideal for thin to medium-gauge sheet metal and provide a quick and cost-effective cutting solution.
1.2.2 Laser Cutting
If precision and intricate designs are paramount, laser cutting emerges as an indispensable technique. Laser cutting utilizes a high-power laser beam to vaporize or melt the sheet metal, creating accurate and clean cuts. This method is exceptionally versatile, allowing for complex shapes and patterns.
1.2.3 Plasma Cutting
Plasma cutting employs a high-temperature plasma arc to melt through the sheet metal. This technique is renowned for its speed, especially when cutting thicker materials. Plasma cutting is a popular choice for industrial applications that require rapid and precise cutting.
1.2.4 Bending and Deburring
In addition to cutting, sheet metal fabrication often involves bending and deburring. Bending refers to the process of shaping the sheet metal into desired angles or curves, while deburring removes any sharp or uneven edges resulting from cutting or bending. Both techniques are crucial for achieving a polished final product.
Chapter 2: Safety Precautions and Guidelines
While sheet metal cutting can be a rewarding process, it is crucial to prioritize safety to prevent accidents and ensure the well-being of everyone involved. Here are some essential safety precautions:
2.1 Personal Protective Equipment (PPE)
Always wear appropriate personal protective equipment, including safety glasses, gloves, and protective clothing. These items provide vital protection against sharp edges, sparks, and potential debris.
2.2 Familiarize Yourself with Equipment
Before operating any cutting tool or equipment, thoroughly read the manufacturer's instructions and familiarize yourself with its functionality and safety features. Additionally, ensure that all tools are in excellent working condition and properly maintained.
2.3 Proper Handling and Secure Workspace
Handle sheet metal with care, as its sharp edges can cause injuries. When working on larger sheets, use proper lifting techniques or equipment to minimize strain on your body. Ensure your workspace is clean, well-organized, and free from clutter, reducing the risk of slips, trips, and falls.
2.4 Fire Safety
Sheet metal cutting processes involving heat, such as laser cutting and plasma cutting, carry a fire risk. Always have appropriate fire extinguishing equipment nearby and familiarize yourself with emergency protocols.
Chapter 3: Choosing the Right Cutting Method
Now that we have covered the basics and safety precautions, it's time to choose the right cutting method for your specific needs. Consider the following factors:
3.1 Material Type and Thickness
The material type and thickness play a crucial role in determining the most suitable cutting method. While shears are effective for thin sheets, laser cutting and plasma cutting excel in intricate designs and thicker materials.
3.2 Accuracy and Precision Requirements
If your project demands exceptional accuracy and precise cuts, laser cutting offers unmatched precision and versatility. Plasma cutting, on the other hand, excels in faster production speed, making it favorable for larger, less intricate projects.
3.3 Project Complexity and Design Flexibility
The complexity of your project and the desired design flexibility will also impact your choice of cutting method. Laser cutting allows for intricate designs, intricate patterns, and complex geometries seamlessly, while shears and plasma cutting are often more suitable for simpler shapes.
Chapter 4: Partner with QuickParts for Your Cutting Needs
When it comes to sheet metal cutting services, QuickParts is your trusted partner. As leading metal fabricators and 3D printing experts, we bring unparalleled expertise, state-of-the-art technology, and a commitment to delivering exceptional results.
4.1 Metal Fabrication Expertise
QuickParts boasts a highly skilled team with extensive knowledge and experience in metal fabrication. We understand the intricacies of cutting sheet metal and can guide you through every step of the process while ensuring your project's success.
4.2 Advanced Cutting Technologies
Equipped with advanced cutting technologies, including laser cutting and plasma cutting, QuickParts brings precision, efficiency, and outstanding quality to your projects. Our cutting-edge equipment ensures accurate, clean cuts resulting in flawless finished products.
4.3 Customization and Design Flexibility
At QuickParts, we understand that each project is unique, requiring customized solutions. With our expertise in cutting techniques and 3D printing capabilities, we offer unparalleled design flexibility, transforming your concepts into reality.
4.4 Commitment to Quality and Customer Satisfaction
At the core of our business philosophy lies an unwavering commitment to quality and customer satisfaction. With QuickParts, you can trust that your sheet metal cutting needs will be met with meticulous attention to detail, superior craftsmanship, and exceptional service.
Conclusion
With this comprehensive guide, we have explored the art and intricacies of cutting sheet metal. From understanding the basics to choosing the right cutting method and prioritizing safety, you now possess the knowledge and insights to excel in your sheet metal cutting endeavors. Remember, partnering with industry experts like QuickParts can further elevate your projects, ensuring precision, efficiency, and remarkable outcomes. Embrace the possibilities of sheet metal cutting and embark on a journey of creativity, craftsmanship, and success.